CNH-Industrial – Electrification and Energy Efficiency Improvements of harvester equipment
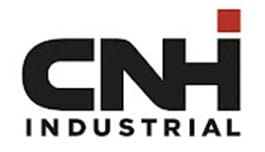
CNH-Industrial
Leon Claeysstraat 3a
8120 Zedelgem
België
https://www.cnhind-belgium.be
jobs.zedelgem@cnhind.com
Contact
Bart Moutton – bart.moutton@cnhind.com
Category
Mechanics
Context
Harvester equipment such as Combine harvesters, Large Square Balers and Forage harvesters typically contain numerous subsystems to process and transport crop inside the machine. Often, they are referred to as ‘Machines on wheels’. Power supply is typically generated by a combustion engine and power is transferred by mechanical and hydraulic drives to the individual subsystems.
These processes all require a certain amount of power at a specific speed. Examples of such drive systems are: belt drives, CVTs, hydraulic drives, gearboxes.
Global climate change and fluctuating fuel and component costs are a continuous driver to monitor and improve power efficiency and total cost.
CNH Industrial in Zedelgem is developing and manufacturing Combine Harvesters, Forage Harvesters and Large Square Balers. Within CNHI, Zedelgem is recognized as a center of excellence for product design.
Objectives
- In this thesis, it is the intention to optimize power efficiency a subsystem of a harvester including dependencies to other subsystems, through simulations. The first step is to do high level (steady state) analysis of potential savings through electrification. The 2nd phase is to dive into dynamic and transient analysis to arrive to component selection for electrified subsystems.
- In this thesis, you will learn to:
- Build the required system models in Matlab Simulink and Amesim, to evaluate the drive system efficiency for different drive architectures.
- Investigate different drive technologies, user profile scenarios and speed ratios to further optimize the drive efficiency
- Evaluate the effect on total cost of ownership of the harvester subsystem.